A Good Counter Argument
- loraborialis
- Mar 23, 2015
- 3 min read

We've been away for about a month, mostly in sick beds or working hard to replenish the tiny house fund. While not much building happened, there was a lot of planning and supplies have been bought (shower unit, toilet seat, propane appliances, etc) so we're now cracking on with the interior.
When we started, we had a pretty good rough plan for the interior, but once the exterior was mostly complete we realised rough just wasn't enough and we had to make some solid decisions pretty quick. We were back onsite last weekend in a flurry of activity. So thanks for being patient, we're proud to start our second wind with a post about our newest edition and major interior feature: our white concrete countertop.

I can hear you now: why on earth did we used concrete?
The title of this post isn't entirely honest since we didn't really have an argument about the counter; the decision was more like a journey. People use all kinds of things in tiny houses for counter tops and we jumped on the live edge wood slab bandwagon first off. It didn't take long to realise that this would be incredibly expensive for the length and thickness we would need as our counter spans the width of the trailer. The hunt was then on for the next best thing.

Concrete is Rory's trade; he's a skilled finisher and it's his family's business, so in the early planning days he lamented that no bit of our tiny house would be concrete. It therefore wasn't long into the countertop journey that Rory started weighing up how he could create a slab thin enough but strong enough to withstand everyday use and moving the house without being too heavy for our trailer. He does like a good challenge.
After a few test slabs at home, he was ready to set up the form. We bought an undermount stainless sink that we slid into the plywood base.
A form was attached around the edges of the base. Styrofoam board was used as a filler in areas of the countertop that did not need to be thick.
The majority of the counter was one inch thick with two inch thick bands around the edges. Wire mesh was used to reinforce the slab so if it does crack, it will still hold together tightly.
We wanted to build in a drain board for our dishes so zinc strips were embedded into a sloping area of the countertop to drain the water and allow dishes to air dry.

Rory did a lot of online research to find the correct sand:cement:rock ratio for a super strong mix. The more water you add to concrete the more workable it is but water also weakens the mix. He found a plasticizer that allows you to have a workable mix while keeping the water:cement ratio low.

We wanted a nice light colour of concrete to keep things bright in the kitchen so opted for white cement. However, it took a good deal of hunting to get the right stuff, since white cement is hard to find and about three times as expensive as regular grey cement.

We used normal river sand in the mix but this darkens the white cement so we used a silica sand and cement mixture, sprinkled dry on the surface of the wet concrete and parged wet on the form face that would later be stripped and trowelled to a smooth finish.
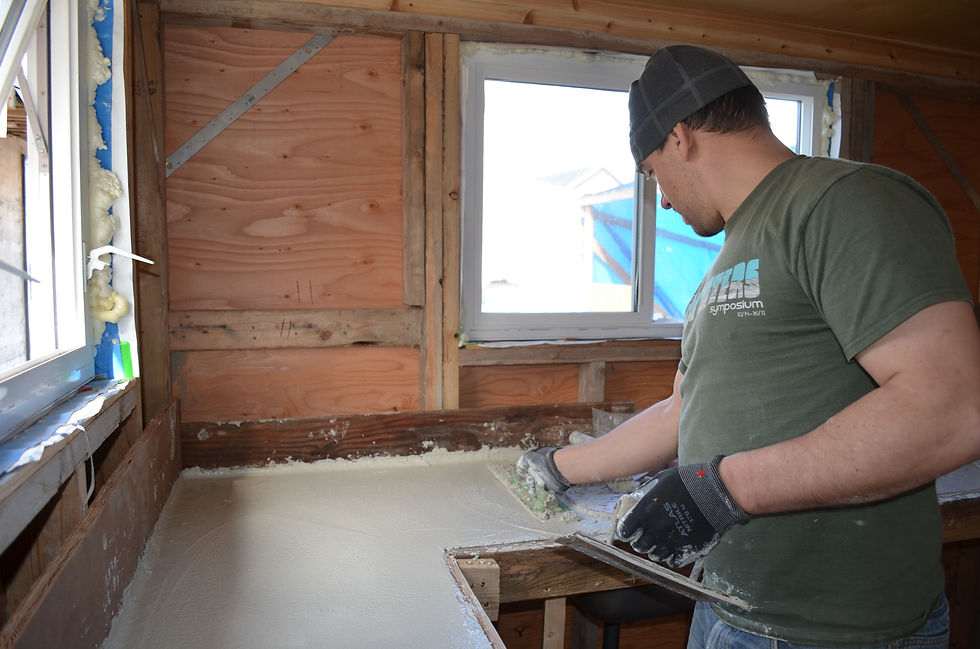
Rory poured the concrete, screeded it and trowelled it smooth. As it set, we pulled the forms off and troweled the edges. At this point it was just a matter of waiting and retrowelling at the appropriate times until the concrete was set hard. We batched the concrete at noon and had a hard trowel finish by 9pm.

And here's our beautiful concrete baby: awesome. The final steps are a couple coats of cure and seal which will keep the concrete from drying to fast and protect from staining, followed by lots of wax that acts as a sacrificial coating. This layer will be maintained over the life of the counter. While it's a weight luxury at about two hundred pounds, our lightweight cedar siding and metal roof package probably make up for it.
Comments